Kent Peterson
Vice President
PE, ASHRAE Presidential Fellow, LEED AP BD+C, BEAP, MCIBSE
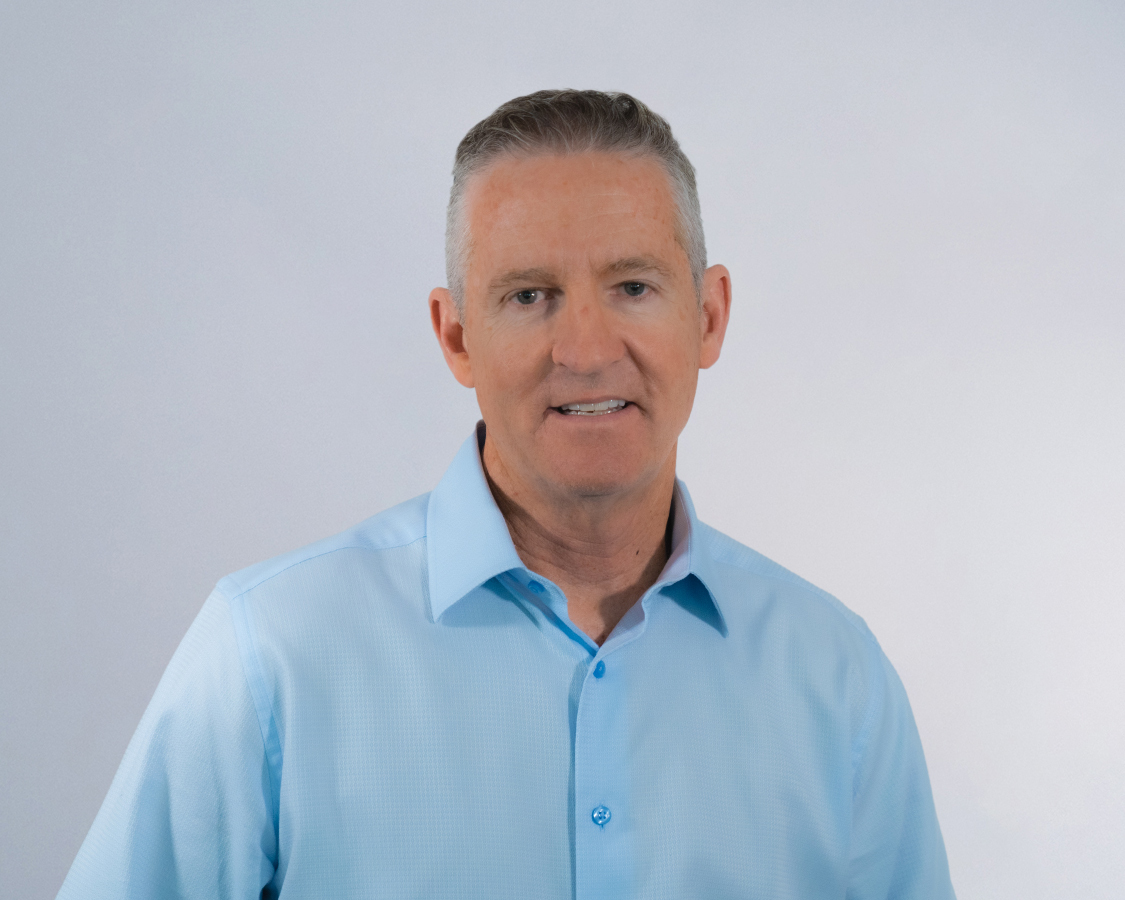
Article Preview
This month’s column explores hydraulic modeling as a tool to optimize hydronic system design. Current hydraulic modeling software can assist designers in predicting hydronic system performance under various scenarios to improve piping system design. This tool can provide the information needed to properly select pumps and control valves. In addition, the computer model provides a good understanding of the interaction of pumps, pipelines, and control valves. Hydraulic modeling software also provides a common basis for design engineers, facility operators and design reviewers to communicate and document fluid piping systems.
In this column, I will point out how relatively simple it is to use this tool to better understand the impact of the initial pipe layout and sizing. As previously stated by Duda,1 reverse return piping can be beneficial for some building layouts, especially in buildings with simple floor plates. This column will focus on hydronic design for more complex floor plates. Taylor and Stein2 have provided valuable insight on balancing variable flow hydronic systems.
Hydraulic Model
Several computer software programs are available for analyzing the hydraulics of HVAC piping systems. The modeling software3 used for this analysis calculates the balanced flow rates and pressures in fluid piping systems, showing how the entire piping system operates. Using the calculated results, one can see the flow rate in each pipeline; the pressure at each pipeline junction; and details of the operation of pumps, control valves, and components. This section briefly describes the calculation methodology used by the program.