Kent Peterson
Vice President
PE, ASHRAE Presidential Fellow, LEED AP BD+C, BEAP, MCIBSE
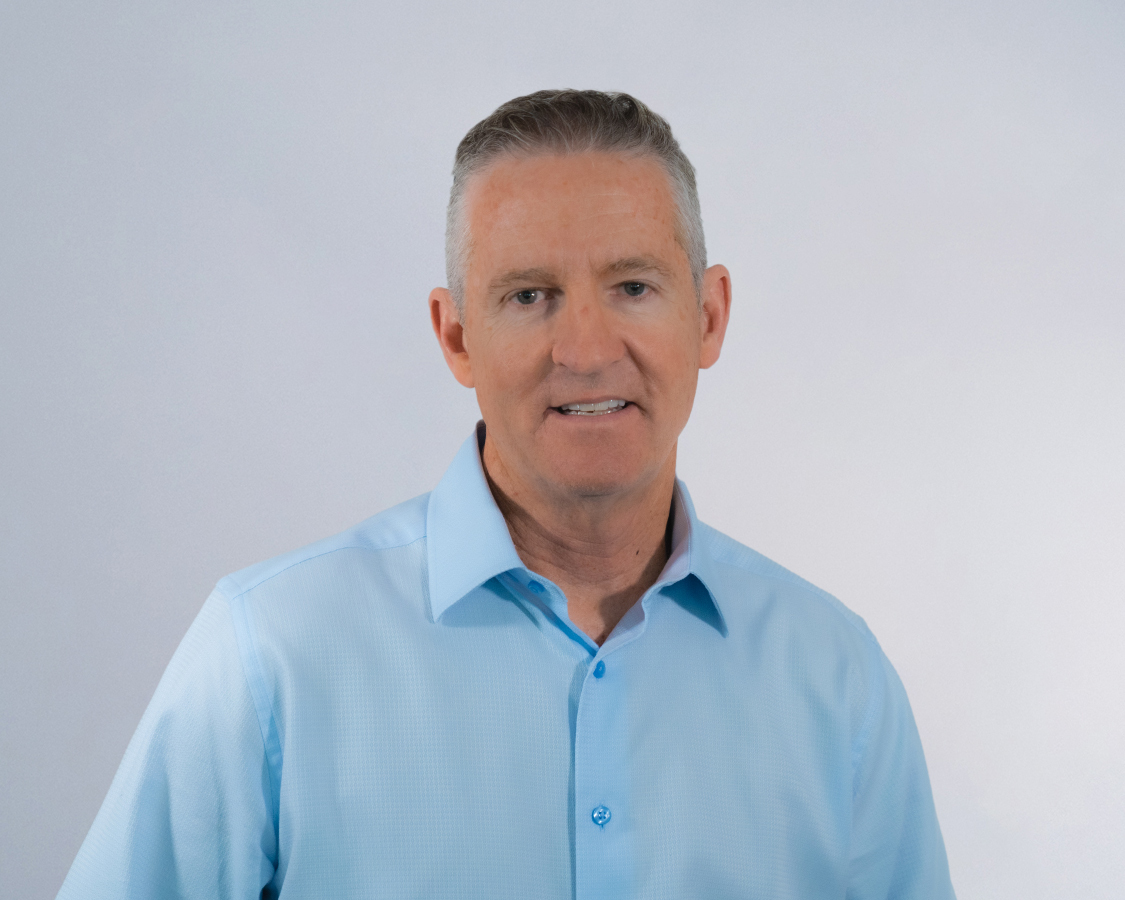
Article Preview
It is important to understand available pipe materials when direct-burying pipe underground. High-density polyethylene (HDPE) pipe has gained acceptance as a non-ferrous alternative to steel pipe in direct-bury applications for chilled and condenser water systems. While steel pipe can deliver unmatched temperature and pressure service levels, properly designed HDPE pipe can deliver corrosion- and leakfree operation.
Some unique challenges require special design considerations due to HDPE piping’s viscoelastic nature, very low material allowable stress, thermal conductivity, large coefficient of thermal expansion, and relatively thick pipe walls. This month I will review these considerations to design and specify underground HDPE piping systems.
Underground Piping Objectives
In the past, most direct-buried chilled water systems used either carbon steel, ductile iron (DI), or polyvinyl chloride (PVC) pipe. These systems and modes of failure were presented in a previous Journal column.1 Ductile iron and 12-in. (305 mm) and larger diameter PVC pipe are typically joined using gasketed push-on joints. These joints are restrained with either concrete thrust blocks or an external bolted-on mechanical coupling. The allowable leakage rate for these types of joints are specified in AWWA Standard C600-102 and AWWA Standard C605-13.3 The author has found that monthly and annual allowable leakage on a large distribution system can be substantial and will result in loss of treated water. Excessive makeup water can also lead to loss of adequate levels of corrosion inhibitor in the circulating water. One objective is to design and install distribution piping that will not leak.